[0004] 从反应原理来讲,最简单的转化方式就是利用集中太阳能产生的热量在超高温下 (通常大于1700℃),直接将水或二氧化碳分解得到氢气和一氧化碳,利用这种技术可以把 能量水平比较低的太阳能转化为高品位的化学能等,实现可再生能源的最大利用。表现为 集中太阳能分解热化学水和二氧化碳,通过这种技术可以得到CO和H2,然后通过费‑托法转 换为液态碳氢燃料,这样就由太阳能转化为了化学能,用以替代化石燃料。但是这种方式对 反应温度有很高的要求,对材料的物理化学性质都有很大的挑战。
[0005] 直接利用聚光器集中太阳能供热以达到水或二氧化碳的分解温度的条件比较高, 而且反应转化效率不高。因此,研究出了两步法高温热化学分解相关氧化物得到燃料气体 的方法。第一步是在较高温度下还原氧化物,释放出氧气,第二步则是在较低温度下通入水 或者二氧化碳,发生氧化反应产生相应的气体燃料。而本发明就是基于这样的原理下而发 明的,在高温下还原产生缺氧的氧化物,然后在管式炉中和水蒸气或者二氧化碳反应生成 氢气或者一氧化碳。
[0006] 目前评估高温热化学制燃料反应的性能方法通常都是实验室规模的,设计出一种 实验方案和相应的一套系统,然后由该系统再对高温热化学制燃料反应进行性能评估,这 种方案有以下不足:
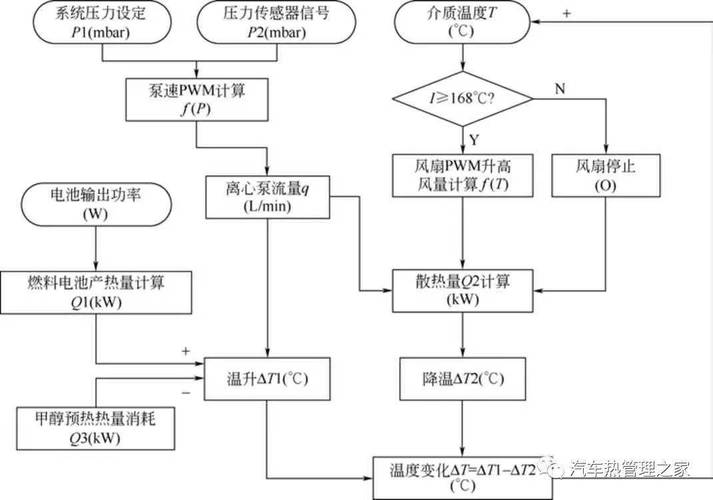
(1)管道路径单一,只能制备氢气或者一氧化碳等其中的一种燃料气体,无法制备 多种燃料,并且大多数实验系统反应温度不够高,无法进行高温热化学裂解氧化物制燃料 的实验。
[0007] (2)管道线路等暴露在空气中,且固定不好,存在安全隐患和操作不便等问题;在 进行反应的操作过程中,比较混乱,没有很好的标注。
[0008] (3)大多都是以气体原料制备燃料气体的裂解反应系统,因裂解水制氢气的系统 更复杂而少有人考虑,难以全方位评估高温热化学制燃料反应的实验性能。
[0009] 此外,本申请人的一篇现有技术(申请号:CN2019106489368)公开一种基于太阳能聚光模拟器的热化学制氢反应性能评估系统及方法,该方法包括原料输入部分,蒸发器/预 加热器,微型多通道反应器,冷凝器,色谱仪,流量管道系统及太阳能聚光模拟器;原料输入 部分包括液体输入部分以及气体输入部分,所述液体输入部分与气体输入部分在蒸发器/ 预加热器前汇聚;蒸发器/预加热器为电加热或太阳能加热的大腔室罐体,其内部设有喷雾 装置;预加热器同时对气体进行初步加热;微型多通道反应器与蒸发器/预加热器以及冷凝 器之间通过管道连接;色谱仪用于检测生成的混合气体成分;所述太阳能聚光模拟器包括 高功率氙灯光源,椭圆形的高反射率反射罩。虽然该文献也是一种评估系统及其方法,其采用的部分技术手段如冷凝器、色谱仪、流量管道系统等硬件设备与本发明相同,但是由于该 现有技术与本发明技术方案以及所要解决的技术问题都不同,因此,本领域技术人员是无法将其应用于本发明以进一步解决本发明所要解决的技术问题的,即该文献没有给出任何 “启示”或“结合启示”来达到本发明的目的。
问题拆分
包括用于输入反应所需气体 的气体预处理部分,用于放置反应物并进行高温 热化学制燃料反应的管式炉部分,用于反应前的 抽真空部分,用于冷凝混合气体的冷凝器部分, 用于分离气体和液体的气液分离器部分,用于防 止有水蒸气进入色谱仪而进行干燥的干燥器部 分,气体成分检测部分。本发明专门为高温裂解 水或二氧化碳制氢气或一氧化碳而设计,产生燃 料气体速率更加稳定并无副产物产生,纯度高; 针对高温热化学裂解水制氢气单独设计水蒸气 发生单元,并且为高温水蒸汽流经的管道加伴热 及保温等措施,防止水蒸气液化。
问题解决
1 . 一种基于高温反应器的热化学制燃料反应性能评估系统,包括气体预处理部分,高 温反应器部分,流量控制及管道部分,冷凝部分,干燥部分,气体成分检测部分;其特征为: 所述气体预处理部分:包括气体直接输入部分以及液相转化气相部分;所述气体直接 输入部分由气瓶提供载气/保护气或者反应气体,气体在混合器中充分混合后进入主管道; 所述液相转化气相部分由载气携带进入主管道; 所述高温反应器部分:实现化学反应的主体,该高温反应器输出端接真空泵以及冷凝 器; 所述流量控制及管道部分:在管道的各个控制节点设置单向开关;不同管段配置相应 的单向阀、真空表、气体流量计、热电偶; 所述冷凝部分:冷凝器与高温反应器之间以不锈钢管相连,钢管上配置单向阀防止高 温气体倒流进入反应器;所述单向阀后配有真空表,用以实时监测反应后混合气体的压力; 冷凝器下方通过不锈钢管道与气液分离器相连,用以收集被冷凝成的液体物质; 所述干燥部分:冷凝后的气体通入到干燥器中,干燥器内部为一到两个干燥柱,干燥器 前面管道配置有单向阀防止混合气体倒流;干燥器后接单向开关与气体流量计相连; 所述气体成分检测部分:干燥后的混合气体通过气体流量计与色谱仪相连,同时配备 计算机以接受色谱仪以及各流量计的数据并进行处理。
2 .根据权利要求1所述的基于高温反应器的热化学制燃料反应性能评估系统,其特征 为:所述高温反应器主体为电加热或者红外加热的高温管式炉,其中内部设计承受高温的 刚玉管。
3 .根据权利要求1所述的基于高温反应器的热化学制燃料反应性能评估系统,其特征 为:所述流量控制及管道部分中的管道种类包括但是不限于耐高温耐腐蚀的不锈钢管,聚 四氟乙烯管,管道之间连接节点以不锈钢紧固的方式保证密封性。
4 .根据权利要求1所述的基于高温反应器的热化学制燃料反应性能评估系统,其特征 为:所述冷凝部分中的冷凝器与高温反应器之间以3mm不锈钢管相连,钢管做保护隔热处 理。
5 .根据权利要求1所述的基于高温反应器的热化学制燃料反应性能评估系统,其特征 为:所述色谱仪检测生成的混合气体的种类和速率,用来对该评估系统的热化学制燃料反 应性能的整体评估。
6 .一种基于高温反应器的热化学制燃料反应性能评估系统的评估方法,包括权利要求 1‑5任一所述的基于高温反应器的热化学制燃料反应性能评估系统,其特征为:包括如下步 骤:
步骤1:将所用催化剂材料放入刚玉坩埚中后放入高温反应器的管道中,填充好催化剂 后,放置好堵头,拧紧反应器管道后的快接法兰;打开循环水泵,并通入冷却水;
步骤2: 打开真空泵将管道进行抽真空操作,然后打开存有载气/保护气的气瓶,利用 减压阀调整压力,利用气体流量计调整气体流量,对实验台系统的各个管段部件进行吹扫; 打开高温管式炉,调整相应的程序控制升温速率至合适温度,同时继续通入载气/保护气, 进行高温热化学制燃料中的第一步还原反应,生成氧气,并计时控制还原反应的进行时间;
步骤3:控制管式炉程序降温,打开存放有反应气的气瓶,通过减压阀控制压力,通过气 体流量计控制反应气体的流量,同时配合载气/保护气的通入,两种气体经混合器后进入主管道,然后进入反应器中,与材料发生第二步氧化反应;
步骤4:未反应完全的气体氧化物,以及反应生成的氢气或一氧化碳,在载气/保护气的 推动下,离开反应器后进入冷凝器中;
步骤5:经过干燥的混合气体通过气体流量计进入气相色谱仪中,对其各组分进行详细 的检测分析,所得数据经计算机处理用于评估整个高温热化学裂解氧化物制燃料系统的性 能与效率。
7 .根据权利要求6所述的一种基于高温反应器的热化学制燃料反应性能评估系统的评 估方法,其特征为:所述步骤3中,当气体进入反应器中,与材料发生第二步氧化反应,其中 反应物如果常温下为气相,可由高压气瓶连接气体流量计控制进入,如果反应物是水的话 则需要通过气体预处理部分的水蒸气发生单元控制产生水蒸气以参与反应。
8 .根据权利要求6所述的一种基于高温反应器的热化学制燃料反应性能评估系统的评 估方法,其特征为:所述步骤4中,当混合气体被冷却,常温下为液态的反应物被冷凝成液体 在气液分离器中被分离收集,其他混合气体进入干燥器被干燥。
9 .根据权利要求6所述的一种基于高温反应器的热化学制燃料反应性能评估系统的评 估方法,其特征为:所述高温反应器的温度区间为700摄氏度至1600摄氏度。
10 .根据权利要求6所述的一种基于高温反应器的热化学制燃料反应性能评估系统的 评估方法,其特征为:以水为反应物,利用基于高温反应器的热化学制燃料反应性能评估系 统制取氢气,并进行相应的性能评估或以二氧化碳为反应物,利用基于高温反应器的热化 学制燃料反应性能评估系统制取一氧化碳,并进行相应的性能评估。