而OTS仿真培训系统能使电厂运行人员熟练地掌握机组启、停和正常运行的全程操作,避免误操作情况的发生,帮助运行人员全面地掌握机组的运行特性,可有效地提高运行人员对机组的调控能力;同时仿真机具有电厂常见事故的模拟功能,事故现象逼真,能够满足运行人员对运行培训、热工保护、调节控制、事故分析的学习要求,以及通过仿真机可以进行机组运行特性的分析研究,验证机组运行操作规程,改善和提高机组的运行操作技术方法,从而有效地提高机组运行的经济性。
目前,企业对安全性、经济性等指标的要求越来越高,OTS仿真培训系统在电厂的安全经济运行方面会发挥出越来越大的作用。
2 基于虚拟DCS的仿真系统结构目前电厂仿真培训系统中最常用的再现DCS的方法有仿真式和全激励式两种。仿真式是根据DCS的组态图、屏幕显示画面及操作,在新的软硬件环境下重新编程,实现其控制策略和人机接口等功能,最后达到与仿真对象一致的效果。这种方式实现成本不高,但有以下不足之处:
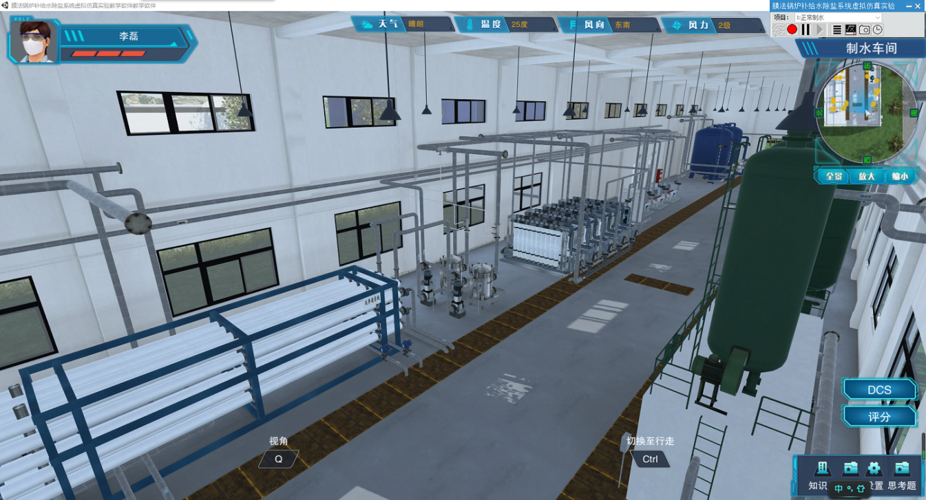
(1)仿真式只能实现控制系统的部分仿真,软件逼真度和可信度不够高,而且在操作员的操作方式、操作习惯方面都会因为二者的开发平台不一样,产生差异,难以实现与现场完全相同的DCS环境,无法达到真正意义上的全仿真效果。
(2)当现场控制系统组态改动时,仿真机的控制系统跟踪修改繁琐困难,扩展性、适应性差。
(3)对热控人员无法进行逻辑修改、控制参数整定等培训。
全激励式DCS省略了输入/输出等卡件,采用真实DCS的硬件软件和网络系统的适当配置来再现DCS,它具有极高的软硬件逼真度,可在仿真机上方便地进行控制算法分析研究及改进工作。这种方式的缺点是软硬件实现成本高、结构复杂、移植性差、与模型系统连接较困难。
鉴于两种方式都存在缺陷,和利时开发了基于虚拟DCS的仿真系统。该控制系统的仿真采用真实DCS技术,以真正的DCS软件及虚拟DPU软件为基础,系统结构、图形组态、逻辑组态完全与现场一致,组态文件可被直接导入到仿真机。虚拟DCS的仿真系统具有仿真精度高、开发周期短、仿真效果好的特点。虚拟DPU技术是指将真实DCS的DPU虚拟软件化,开发的虚拟DPU软件能够完全代替真实DPU的计算、通讯功能,从而降低用户的使用与维护成本。
图1 传统仿真机与虚拟DCS仿真机比较
3 仿真系统硬件组成仿真系统由仿真主机(模型站兼教练员站)、DCS&DEH操作站、就地操作站、DCS站(DCS服务器兼工程师站)、虚拟DPU站、网络设备等组成。DCS操作员站的数量根据用户需要配置,并且可以随时扩充,其硬件构成如图2所示:
图2 仿真机系统硬件结构图
4 仿真系统软件组成及功能仿真系统软件包括操作系统软件、仿真支撑平台软件、数学模型软件、教练员功能软件、DCS操作员站软件、多媒体仿真软件、DCS工程师站软件、就地站及虚拟盘台软件等几部分,图3所示:
图3 仿真机软件构成
4.1 系统软件
主机和各操作站均采用Windows操作系统,具有界面友好、开放性高、可适用于不同机型的特点。
4.2 仿真支撑平台软件
仿真支撑平台软件是介于仿真系统和计算机操作系统之间的可视化仿真支撑系统,运行在Windows操作系统上。其主要特点如下:
(1)实时网络数据库:专门为大型仿真系统设计的网络实时数据库,可以管理变量达数百万个、数据上千万个,可实现多个模型的分布式计算、动态数据显示与在线数据修改,满足大型实时仿真系统的开发和运行的需要。
(2)数据可视化:提供多种数据可视化方式,如表格、曲线、流程图、直方图和虚拟盘台等。
(3)图形化建模:用户可以方便地利用系统提供的可视化单元,完成电站所需的运行画面的组态,提高工程化水平、提高开发效率。
(4)在线调试:在各种显示方式下,都可以对数据库中的任意数据进行在线修改。
(5)协同开发:支持多人在网络环境下的程序协同开发,提供了从程序编辑、变量扫描、编译、连接到运行、调试等全过程的支持。
(6)进程控制:完整的指导教师工作站功能,主要包括模型的运行与停止、冻结与解冻、故障设置、工况保存、运行状态的显示。
(7)仿真精度高:具有高精度的仿真周期,最小仿真步长可以达到10毫秒,数据刷新时间步长可以达到50毫秒。
(8)多流程仿真:多流程支持功能,可以在一套硬件系统上同时开发或运行不同的仿真系统,或者同一套仿真系统的多个实例。
(9)支持OPC协议。
(10)可视化图形建模系统与强大的在线调试功能,大大提高了开发速度、降低了开发难度、缩短了开发周期、提高了系统可维护性。
4.3 数学模型软件
数学模型根据工程实际订制开发,以基本物理原则为基础,以实际机组的资料为依据,采用图形化建模方式完成。所建模型精度高,能完整地描述机组的静态和动态的全过程,包括从锅炉点火、升温、升压等各种工况下的启动、并网、升负荷以及正常停机和各种事故现象。数学模型软件由以下几部分组成:
(1)锅炉系统数学模型软件;
(2)汽机系统数学模型软件;
(3)电气系统数学模型软件;
(4)控制系统数学模型软件;
(5)其他系统数学模型软件;
4.4 教练员站功能
仿真机的教练员站是多功能、多用途的培训训练中心。在教练员站软件和硬件配置基础上成为仿真机运行的最主要的人机界面,在实时情况下进行教练员与仿真机之间的信息传输。所完成的仿真培训的基本任务是:
(1)教练员能方便地控制和监视学员的操作;
(2)教练员根据学员的业务能力选择组合项目;
(3)教练员和软件工程师可由教练员台访问实时数据库;
(4)采用文字、数据、表格、图形等方式显示,借助彩色LCD,键盘等实现。
教练员站主要用来设定各种工况和事故,对学员进行培训。仿真机的主要功能都是由教练员通过教练员工作站发出指令来实现的。教练员站功能软件被集成在仿真支撑平台软件中,运行于模型服务器上。
教练员功能用于控制整个仿真系统的运行,它主要包括以下项目:
(1)启动和停止
启动功能自动装入仿真程序,使系统进入仿真机运行状态。停止功能使教练员方便地停止仿真机的运行。
(2)初始工况的选择
教练员可方便地选择所需的初始运行工况,并使仿真机的运行状态处于已选择好的工况点。用户可以自己设置任意多的初始工况。
(3)冻结与解冻
冻结功能允许教练员在仿真机运行的任何时刻冻结,使之处于冻结状态,冻结时刻存在的所有参数与状态保持不变。解除冻结使系统重新进入运行状态。
(4)工况存储和调用
工况存储和调用功能允许在仿真机运行过程中随时记录当前工况和调用任何一个已经存储的工况。
(5)监视变量
在仿真机运行中,教练员可以通过多种方式显示模型中的任意变量,以监视模型的运行状况。
(6)设置故障
允许教练员设置单个或成组故障。
(7)参数修改
允许教练员修改仿真机组的外部参数。
4.5 DCS工程师站
工程师站用于程序开发、系统诊断、控制系统组态、数据库和画面的编辑及修改、控制逻辑编译和下装。同时工程师能实现操作员所有的监视和操作功能。
4.6 虚拟DPU软件
虚拟DPU软件完全实现真实DPU的计算与通讯功能,只需运行在普通计算机上即可,不仅提高了仿真系统真实度和拓展了仿真系统功能,同时不需采用真实的DPU硬件,从而大大地降低了仿真机的使用与维护成本。正是由于采用了虚拟DPU技术,仿真系统才能够使用真正的DCS软件,才是真正意义上的虚拟DCS仿真机。
4.7 DCS/DEH操作员站功能
操作员站用于完成实时数据采集、动态数据显示、过程自动控制、顺序控制、高级控制、报警和日志检测、监视、操作,对数据进行记录、统计、显示、打印等处理。对于虚拟DCS仿真机,采用真正的DCS操作员站软件,其功能与真实DCS完全一样,因此DCS的画面显示、操作界面以及用户感受等都与现场完全一致。
操作员站的基本功能如下:
(1)监视系统内每一个模拟量和数字量及所有工艺流程,以列表的形式查看组成一组的点的信息;
(2)显示并报警发声,包括工艺报警、设备报警;
(3)显示操作指导、操作记录;
(4)建立趋势画面并获得趋势信息;
(5)打印报表;
(6)屏幕拷贝;
(7)自动和手动控制方式的选择;
(8)调整过程设定值和偏置等;
(9)历史数据查询;
(10)查看日志信息。
4.8 就地操作站功能
就地操作站软件采用了与DCS操作员站相同的软件,其画面显示、操作界面以及用户感受等都与DCS操作员站完全一致,使用户更容易接受和习惯,同时也具备了DCS操作员站与就地操作员站之间任意切换的功能。
就地操作站功能软件主要实现电厂中需到现场进行就地操作,以及实现各种保护柜、励磁柜,快切装置柜、直流柜等虚拟盘台上的操作。
5 应用实例5.1 项目背景
陕西某电厂2×600MW机组选用OTS作为仿真培训平台,现场位于陕西省榆林市。项目以其电厂#3机组为仿真对象,DCS采用改为:HOLLiASMACSV6系统,锅炉是由上海锅炉厂有限公司制造的亚临界参数Ⅱ型汽包炉,汽轮机采用上海汽轮机有限公司设计制造的亚临界、一次中间再热、单轴、三缸四排汽、直接空冷凝汽式汽轮机。发电机采用上海汽轮发电机有限公司生产的QFSN-600-2型600MW汽轮发电机。仿真系统采用虚拟DPU技术来实现,工艺模型与虚拟控制器通过OPC通讯实现数据传送。
5.2 项目仿真范围及功能
整个仿真系统涵盖了运行操作人员启停机需要操作的主要设备,以及从冷态到最大连续出力运行的所有运行方式,保证在整个运行范围内的连续性。仿真机还能仿真包括涉及故障、非正常操作事件和事故及相应的瞬态过程。其功能如下:
(1)操作过程与现场真实操作方式一致,实现了在不影响正常生产运行的前提下,提高了运行操作人员的操作水平;仿真采用虚拟DPU方式,可同时对运行人员、热控人员进行培训;
(2)DCS组态无需经过任何修改,能被直接用于仿真机,缩短了调试周期;
(3)OTS仿真培训系统设有故障点加载功能,培训教师可在正常运行中随时加入故障点,以达到提高运行操作人员的事故处理能力;
(4)采用与现场一致的DCS组态逻辑,可以通过仿真平台测试、优化改造方案,试验成功后,再将修改后的组态导入到真实DCS软件中,从而降低逻辑变更带来的潜在风险。
5.3 应用创新性
(1)先进的虚拟DPU技术
实现DCS分散处理单元的仿真,模拟真实DPU的运算过程;与真实DCS软件无缝对接,实现现场DCS工程文件和仿真DCS工程文件相互导入;模拟DCS主控、模块、通道等仪控故障;实现真实DCS仿真系统下的自由分组培训。(2) 智能重演
历史重演:回放现场DCS历史数据进行事故分析;数据重演:在仿真系统上还原事故操作过程,制定反事故规程;操作重演:支持随时暂停、回退进行新操作,推演正确操作方式。图4 虚拟控制器
(3) DCS数字孪生
真实控制机柜1:1建模,实现电子间三维漫游;DCS模块拆解、安装与接线,实现自感知硬件设计与验证;与真实控制器同步通讯,实现数据联动;DCS故障诊断与演练,实现故障可视化。图5 三维电子间
6 结束语由于目前火电厂自动化程度大大提高,运行人员操作机会相对减少,一旦发生故障和事故时, 需要能够进行及时、正确的处理。在短暂的时间里,依据机组运行经验, 正确判断出事故现象及故障原因, 进行合理的操作与协调, 排除事故现象, 保证机组安全运行。为了进一步提高运行人员对事故状态的快速应变及处理能力, 通过配置与单元机组完全一致的仿真系统, 运行人员可通过机组在各种工况下的启动、停止、正常运行操作, 加深对系统的认识, 提高准确判断、处理事故的能力, 并提高事故情况下操作的正确率。同时也为各种工况下运行技术的分析和控制系统研究创造了实时和在线的环境, 应用基于虚拟DCS的仿真系统可进行发电机组运行方式研究, 如机组启、停、变工况等可能运行方式的研究, 为提高机组运行的安全性、可靠性、经济性以及确定相应的规程和标准提供依据。
摘自《自动化博览》2020年8月刊