生产效率提高了30%,7.5秒便可生产一个ABS电机,操作人员减少80%,36道工序、39个工位只需2个人操作,一个人负责上料、一个人负责成品质检,质量损失减少了30%,换型时间减少了30%
长沙全媒体 伍玲 通讯员 张卉
8月17日,博世长沙又迎来一批来自北京、上海的参观者。
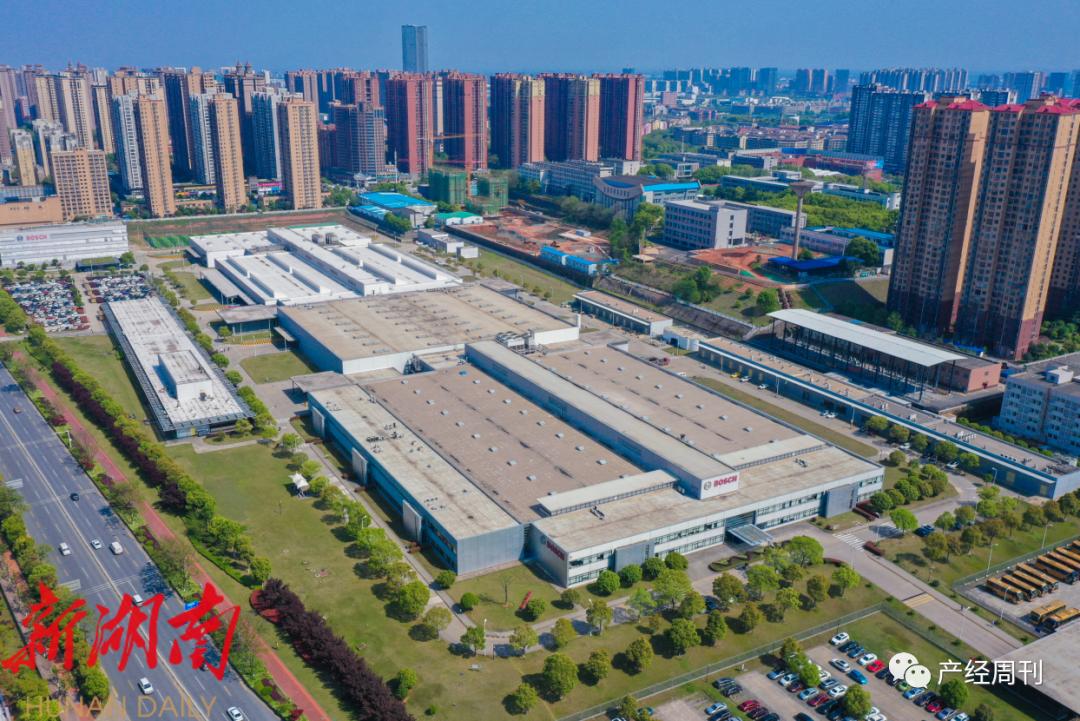
看到一波又一波的“取经者”,刘瑜的记忆回到了几个月前那个令人兴奋的时刻。
3月30日下午,世界经济论坛对外公布2022年度第一批13家“灯塔工厂”名单,博世汽车部件(长沙)有限公司名列其中,成为湖南本土首家荣获“灯塔工厂”称号的企业。
得知消息的那一刻,刘瑜激动得站了起来,眼眶红润。办公室里响起一阵阵欢呼声和掌声。
掌声是同事送给刘瑜和团队成员的。身为博世长沙工业4.0高级经理,刘瑜和团队成员闯过了一关又一关,终于梦想成真。
此次灯塔工厂评选,全球参选企业有1000多家,入围者可谓百里挑一,博世长沙为何能脱颖而出?
设备互联 让机器“活”起来
一切都要从2015年开始说起。
“那一年有两个契机,一个是国务院印发了《中国制造2025》,长沙发布了全国首个智能制造三年行动计划。”博世长沙生产技术总监张毕生回忆说,当时智能制造概念大热,但社会普遍对智能制造、工业4.0的概念语焉不详,更不清楚智能制造的生产线是什么样子。
为了拥抱智能制造,不少长沙企业跑到外地“取经”。
在长沙建一条工业4.0的生产线,让企业就近学习!
这一任务就落到了博世长沙,并从当年10月启动。
实际上,博世长沙自己也渴望已久。原来,自2006年落户长沙以来,博世长沙产值持续增长,产线增至100多条,不少设备历经岁月磨洗,开始变得老旧。
张毕生告诉,一切都是从零开始,团队摸着石头过河,在经过3个月的研究、摸索后,工业4.0生产线概念设计蓝图才正式出炉。
设计中,博世长沙首先考虑的,是要让机器“活”起来。
怎么才算“活”了?“互联互通,让原本的机器信息孤岛实现连通。”刘瑜解释道。
于是,博世长沙买来智能传感器,安装在设备上,捕捉设备运行动作,包括振动、扭矩、电压和电流等一系列数据。
“我们把互联程度分为了四个等级。”刘瑜告诉,从设备、产线、车间再到公司,均实施了不同程度的互联,尤其是车削等核心工艺、关键设备的互联。
而对于一些机械、重复的工位,则采取机器代人,为此博世长沙几年来投入100多台机器人,提升产线和车间的自动化水平。
经过一年多的建设,2016年底,湖南首条工业4.0生产线在博世长沙正式投产。
这条产线有多厉害?几个数据可见一斑:生产效率提高了30%,7.5秒便可生产一个ABS电机,操作人员减少80%,36道工序,39个工位,只需2个人操作,一个人负责上料,一个人负责成品质检,质量损失减少了30%,换型时间也减少了30%。
几年下来,博世长沙互联的设备、产线越来越多。“机器人互联率逾80%,预计2023年可实现100%;60多条产线实现了互联,整个公司互联率超过80%。”刘瑜列举了3个数据。
数据挖掘 发现“富矿”创造价值
“灯塔工厂”项目旨在遴选出在第四次工业革命尖端技术应用整合工作方面卓有成效、堪为全球表率的领先企业,被誉为第四次工业革命的指路明灯。按照评选标准,每个企业必须有5个及以上数字化制造应用案例,且具备世界领先水平。
博世长沙此次申报方案中,最为打眼的当属人工智能驱动生产能源管理、机器人实时管理系统、数据智能决策、全透明的生产现场管理和端对端智慧物流中台等5个应用案例。
“几个应用案例能够实现,最核心的资源是数据。”3年前,夏晓毛来到博世长沙担任数据科学家,成为企业第一个专家级数字化人才。在他眼中,数据对数字化而言,如同石油一般重要。
车削工艺是生产数据的富矿。在博世长沙看到,一台台设备呈岛式设置,布局十分紧凑。“一台设备一个月就能产生100G的数据。”夏晓毛指着跟前的设备介绍,车削设备加装传感器后,以数千赫兹的频率采集车刀振动数据,然后从中提取上百个特征用于数据模型。
“数据采集还要经过处理、建模和验证与应用,最难的就是建模。”在夏晓毛看来,要把一线工程师的经验转化为数据模型,特征指标选择,探寻合理区间,需要不断尝试。“曾经为了建一个数据模型,我们团队花大半年时间却没有进展。”
皮带是博世长沙最常见的一种易耗品,每月费用在14万元左右。以前更换,全凭经验。但也有局限性,因皮带生产批次、产品质量差异等因素,会让皮带的使用寿命不尽相同,这就会出现部分皮带还未到使用时间就被更换的情况,而且一旦20多米长的皮带断了、卡了,需要停机三四个小时进行更换,带来难以估量的产量损失。
“我们先后从声音、磨损图像、振动等维度去分析皮带磨损情况,最后发现通过振动指标判断是最佳的。”夏晓毛说,团队运用大数据技术、机器学习算法对皮带等易耗品进行深入分析,并建立高精度易耗品使用寿命预测模型,以此给出易耗品最佳更换时间。
如今,该数据模型上线后,帮助博世长沙提升皮带、焊接电极、车削刀具等生产易耗品30%以上的使用寿命,并节省50%的更换时间。
事实上,数据的流通和利用在博世长沙无处不在。在物流端,从原材料供应、运输、内部流转到生产及货物出厂,整个流程都由物流中台通过实时数据连接。而在流通的过程中,只要监控到数据异常,系统就会及时报警。
博世长沙原物流总监文天俊介绍,该平台帮助博世长沙节省了30%的物流成本和15%的库存周转天数,使生产周期大大缩短,在提高生产效率的同时,其创新的方案和系统创造了博世全球多个第一,并进行了推广。
持续革新 向“未来工厂”迈进
几年来,数字化的浪潮浸润着博世长沙的每一个角落,通过渗透率达到100%的可视化数字化车间管理,博世长沙在内部实现了涵盖流程、原料、设备、人事、文件系统等多个业务环节的精益日常管理。
“专家级数字化人才有10余人,玩家级数字化人才超过400人。”在博世长沙生产运营副总裁邓宁的手机中,看到一个名为数字化夏令营的微信群,入群人数有460多人。
比人数增加更重要的是员工思维方式的转变。“不少员工看到数字化的成效,都积极主动投身数字化浪潮,纷纷利用业余时间设计数字化解决方案。”邓宁说。
这得益于博世长沙设立了一种类似于揭榜挂帅的机制,只不过提出需求的是员工:结合日常工作,博世长沙员工会提出数字化升级需求,再由公司筛选、审核,给予研发资金。
“大家热情都很高,目前开发了好几款软件。”邓宁说,目前博世长沙正在使用的一款智能报表系统就是由员工自主研发,另外一款报价系统让原本2周的报价周期缩减到1天。
看到公司几年的数字化革新,博世长沙总经理魏彦更是喜上眉梢。对于“灯塔工厂”的概念,他更愿意描述为“未来工厂”。
“我们将会继续致力于技术革新,深度聚焦生产流程自动化、智能化、数字化的全面实现,构建智能制造价值链及智能生态系统,向‘未来工厂’的建设目标持续迈进,助推中国先进制造业领跑世界。”魏彦说。