机器人设计师可采用 Adams 多体仿真(MBS)软件对整个机器人机构的瞬态动力学行为及控制算法进行仿真,从而提高产品性能。
机器人设计师面临哪些挑战?
设计师需要用尽可能低的成本,获得尽可能高水准的速度、准确度、耐用性及其他性能参数。能否赢得订单的差别往往不过是速度上 5% 的优势,因此机器人设计师需要突破设计过程的束缚。
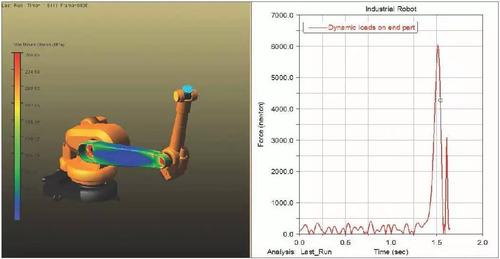
目前机器人设计师所面临的另一个挑战是了解机器人各种关节的受载大小。关节作用力在很大程度上取决于机器人的轴承和横梁的刚度,因此传统的设计工具无法提供准确的预测。
同时,在当今竞争日趋激烈的环境下,机器人控制算法的设计也变得越来越关键、越来越困难。为满足交货日程表,通常需要在设计机器人本身的同时设计控制算法,但对于做出完美设计决策所需的动态因素,现有的设计方法所能提供的信息却寥寥无几。
可将 Adams 模型与控制系统模型进行协同仿真
Adams MBD 软件可在样机阶段之前预测机器人的动态性能
Adams MBD 软件超越了传统的机器人设计工具,它提供了大位移动力学仿真功能,可全面捕获真实环境中的复杂性。Adams 可简化刚体与柔性体、齿轮、轴承、电机、关节及其他机器人部件的动态性能建模,从而克服运动学解决方案的局限性,在处理与机器人互动的对象时更是易如反掌。因此,Adams 使机器人设计师能够在设计过程初期、得到样机之前,将其产品作为一个整体系统对其动态性能进行评估。
Adams 提供了各种柔性体建模选择,可准确地了解机器人任何部件的动态行为。
Adams 如何设计性能更出色的机器人
考虑部件的柔性,计算机器人手臂轨迹
Adams 能整合柔性体与齿轮,仿真得到部件变形,与传动方法相比,能够更准确计算机器人手臂的轨迹。由于将零部件变形整合到动力学模型中,还使设计师能够准确地预测所有机器人零部件承受的负载。通过增加电机扭矩并降低零部件重量,机器人设计师可使用 Adams 仿真尽量提高机器人的速度,而且既不会超过规定的加载值,也不会产生剧烈振动。如果特定零部件负载过大,机器人设计师可修改机器人的设计或控制算法,并确定其对零部件加载的影响。在出现碰撞时,机器人设计师还可以轻松地确定作用到操作员身上的负载,以简化协作机器人的设计流程。
MBD 预测机器人的系统级振动
确定齿轮啮合间隙对移动轨迹的影响
同时,Adams 还能使机器人设计师能够确定机器人设计的固有频率,并预测具体应用中所经历的振动水平;机器人设计师还可以在设计初期精调控制算法,将机器人臂和传动机构的动态响应考虑在内,从而提高机器人的定位精度;Adams 还使机器人设计师能够在设计初期,通过对机器人手臂移动时,电缆的变形和电缆运动规律进行仿真分析,从而评估不同的电缆导引及管理方式的性能;还可以使用 Adams 开发可管理复杂包装操作的机器人,并能配合所开发的新包装款式。