故障电弧是低压配电网及楼宇电路中常见却不容易发现的现象。低压配电网线路长时间高负荷运行,线路老化、绝缘层破损等情况都易引起故障电弧。如今故障电弧已成为电气火灾产生的主要原因之一,为了防范此类电气火灾的发生,常采用加装相应保护产品的方法。保护产品的关键技术之一是故障电弧检测,因此产品在研发阶段都进行电弧故障检测实验。美国推出UL1699故障电弧保护产品的安全标准,并强制家庭卧室安装电弧断路设备(arc fault circuit interrupter, AFCI)。
国家标准GB 14287.4—2014《电气火灾监控系统 第4部分:故障电弧探测器》和GB/T 31143—2014《电弧故障保护电器的一般要求》分别对此类实验做出明确规定,包括故障电弧模拟方法及不同实验电流中故障电弧最大燃弧时间的要求。电弧故障发生装置是一种故障电弧模拟所需的设备。故障电弧发生装置由一组动、静电极组成,其中静电极主要材料为碳棒,动电极主要材料为铜棒,当两电极接触良好并通过电流后,动电极开始横向移动与静电极分离,直至产生电弧。两电极的分离距离和拉弧速度直接影响故障电弧模拟效果。
基于此,本文研制一种基于双闭环控制策略的交直流串联故障电弧模拟装置,通过改进装置结构和控制方法来提高故障电弧模拟的成功率。
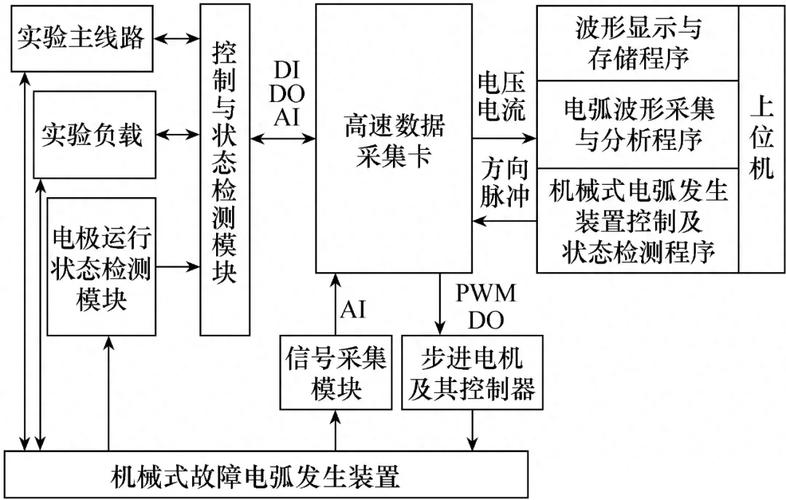
1 设计思路
故障电弧模拟装置结构采用模块化设计,包括上位机和下位机两部分。上位机设计包括电弧发生装置控制模块、电弧波形数据采集与分析模块、传感器状态检测模块等。下位机平台由高速数据采集卡、机械式故障电弧发生装置、控制与状态检测模块、信号采集模块、实验线路等硬件设备组成。装置整体结构框图如图1所示。
图1 装置整体结构框图
该装置燃弧机构的设计理念基于传统拉弧装置,即利用两个通电电极拉弧。与传统拉弧装置不同的是,本文设计的故障电弧发生装置不仅可手动控制,还可以步进电机为动力装置,通过步进电机旋转带动可移动电极运动,实现两电极的接触和动态拉弧。高速数据采集卡是整个装置的控制中枢,计算机通过高速数据采集卡获取下位机运行状态并进行信号采集,同时发送指令至下位机,根据上位机状态使下位机进行相应动作。
控制与状态检测模块基于高速数据采集卡设计,所述高速数据采集卡安装在计算机高速串行计算机扩展总线标准(peripheral component inter- connect express, PCIE)接口上,作为输入输出模块,可以输出控制命令并获取实时装置运行信息。
上位机通过多功能高速数据采集卡的脉宽调制(pulse width modulation, PWM)脉冲输出通道向动力系统传送速度控制命令,通过数字信号输出(digital output, DO)通道向动力系统传送方向控制命令,通过模拟信号输入(analog input, AI)通道从数据采集模块接收执行机构运行状态信息,运行状态信息包括两电极之间的电压波形数据及电极流通的电流波形数据。
本文控制算法基于压力值变化量控制电机方向进而控制电极左右移动,但由于两电极接触、摩擦的过程,导致实际电机移动距离与设定距离产生偏差;特别在低电流情况下,挤压、摩擦现象更加频繁,电机移动距离、移动速度会产生较大误差,无法按照预定速度、预定距离移动。
故步进电机采用闭环控制策略,经过比例积分微分(proportional integral differential, PID)对电机移动过程进行控制,保证速度和位置的准确性。实际应用中,为了同时保证电极移动距离和速度满足故障电弧模拟需求,避免因步进电机失步导致电极位移量不足或速度过快等问题,本文装置采用双闭环控制策略,以位移环PID的输出量作为速度环的期望值,该数值与速度实际值的偏差作为PID输入量传入速度环,从而实现速度、位移双闭环控制,以解决上述问题。
系统信号采集模块的设计基于电压、电流传感器。与传统信号采集装置不同的是,本文设计的故障信号采集装置通过设计多档可选的采集电路配合高速数据采集卡模拟信号输入通道的功能实现。上位机信号采集程序可准确采集细微的信号变化量,并实时显示。
2 硬件设计
2.1 机械结构设计
机械式故障电弧发生装置按照国家标准设计了串联故障电弧的点接触装置,故障电弧实验平台如图2所示。该装置的机械部件由固定电极、丝杆、移动电极、压力传感器、光电传感器、步进电机和电极安装台组成。
可移动电极和固定电极分别安装在固定支座和移动支座上,实验线路分别连接至两电极的一端,并且与实验主线路连接,从而实现电极的通、断电。同时,步进电机是装置的动力来源,电极底座安装带丝杆的步进电机,其旋转时通过丝杠牵引可移动滑块运动,进而带动移动电极水平移动,实现与固定电极的接触和分离。
为了避免可移动电极运动超行程导致机械部件受损,在左右移动极限位置安装光电传感器,并在可移动滑块上安装遮光金属片,当电极移动至左右限位光电传感器位置时,将触发光电传感器输出模块信号改变,该信号经高速数据采集卡传递至上位机作为状态反馈指令,从而控制步进电机停止运行,确保实验安全。此外,为了确保通电前,两电极能够可靠接触,在固定电极的端部安装有压力传感器,装置通过检测可移动电极压力值是否达到阈值来判定两电极是否完全接触,并通过电压波形适当进行手动调整。
图2 故障电弧实验平台
2.2 主线路与控制线路设计
在设计电气控制线路时,基于电路可靠性原则,综合考虑系统的总体布局、配电方案、接地线路等因素,确保线路电源的负载量在预计范围之内。此外,还需考虑系统线路的其他问题,如电弧发生时,系统发热,线路温度变化会使传感器产生误差;扩展接口与大功率用电器连接时,拉弧线路对控制线路产生影响等问题,避免可能发生的事故和隐患,提高系统安全性和稳定性。
由于故障电弧模拟时系统会发生电压、电流突变,且长时间产生故障电弧时会伴随系统发热现象,拉弧线路高电流等级时尤为明显,因此考虑到热稳定性和系统安全性,装置采用主线路与控制线路分开设计的方案,装置线路原理如图3所示。主线路经电源模块为拉弧线路供电,拉弧线路并联不同阻值负载,产生不同等级电弧电流信号。控制线路经独立电源模块为信号采集模块、状态监测模块和步进电机控制模块独立供电。
图3 装置线路原理
为了实现对不同电流等级故障电弧的模拟,装置设有五个档位的电流信号(0.2A,0.8A,1A,2A和5A)控制开关,并可通过上位机进行排列组合式控制,其通过并联方式相互叠加,实现线路对不同等级电流信号的控制。
2.3 信号采集电路设计
为了确保装置在不同电流等级下进行实验时信号采样的精度,在设计信号采集电路时,采取多档位可选切换的设计方案。目前,装置的电流采集电路有三档,分别为0~5A、5~25A、25~100A。电流信号采集电路如图4所示。
对于0~25A的实验电流,选用莱姆LA25—NP电流传感器进行设计,该传感器可通过不同的连线形式实现不同等级的电流采集。其中,0~5A档位的实验电流采集电路如图4(a)所示,电流通过电流传感器对线路电流信号进行缩放处理后经采样电阻R11转换为电压信号,最终上传至高速数据采集卡中;5~25A档位的实验电流采集电路如图4(b)所示,与0~5A档位不同的是,通过更改信号输入接线方式,改变电流传感器信号缩放比例,进而完成更大档位信号采集;25~100A的实验电流采集电路选用莱姆LA100—P传感器进行设计,如图4(c)所示。
图4中R11、R12、R14为采样电阻,将电流传感器二次侧输出的电流信号转换为电压信号,并连接至高速数据采集卡模拟量输入通道。
图4 电流信号采集电路
电压信号采集电路选用LV25—P电压传感器进行设计,该传感器的工作原理为由霍尔元件检测到磁场后驱动一个运算放大器,其中一、二次电流比为10mA/25mA,这样电压比就由两边的电阻确定,电压信号采样电路如图5所示。
为了避免电阻因功耗过大、长期通电时的温升影响其精度,采样电阻选用高精度低温漂精密电阻,并且采用串并联的方式来降低每一个电阻的工作电流,如图5中的R2、R3、R4、R5所示。由于LV25—P仍然为电流-电流型传感器,其二次电流通过200W的采样电阻R13转换为电压。
将不同的传感器电路二次侧输出的电压信号分别连接至高速数据采集卡的模拟量输入通道,配合上位机程序可以实现不同实验电流下不同采样电路的自主选择。在实验前设置好当前实验电流,实验过程中上位机平台自动读取对应量程通道采集的信图5 电压信号采集电路号,并将该信号显示在人机交互界面上。
图5 电压信号采集电路
3 上位机设计
3.1 拉弧电极控制策略
拉弧电极以步进电机作为动力装置,选用42型闭环步进电机,步距角1.8°,但实际拉弧时为了能够精确控制可移动电极的移动距离,步距角需小于此数值,故将步距角进行细分处理,本文装置采用8细分处理。步进电机联动丝杆选用导程为10mm的2510型丝杆,即丝杆转动一周电极移动10mm。
该丝杆为单头丝杆,导程数值与螺距数值相同,即步进电机转动一周带动丝杆也转动一周,由此得出电极前进10mm需1600个脉冲。步进电机的控制采用基于PID的双闭环控制策略,包括位移环、速度环,前者为外环,以丝杆可移动范围为初始输入量,位置调节器输出位移变化量;后者为内环,以位移偏差量作为输入,用于调节步进电机运转速度。基于PID的闭环控制框图如图6所示。
图6 基于PID的闭环控制框图
位移环采用位置式PID控制,如式(1)所示,将设定距离通过上述硬件转化为所需脉冲个数,将所需脉冲个数经过倍频系数、减速比等处理后作为目标值,所需目标值与当前实际值的偏差传入PID控制器,PID控制器将位置误差进行积分、微分等处理后输出结果,此结果用来更新PWM脉冲输出个数和运转方向,以控制步进电机旋转周数,限制电极间距,从而进行位移控制,此结果也作为速度环的输入参数。
式(1)
式(1)中:e(k)、e(k-1)分别为第k、k-1采样时刻PID控制器输入信号偏差值;KP、KI、KD分别为PID控制器的比例系数、积分系数、微分系数;为误差的累加。
实际使用中,由于积分项的作用,速度误差不断累积,会产生积分项达到饱和的问题。当积分项达到饱和时,如果出现反向误差,系统需要时间退出饱和区,致使装置不会在第一时间对反向误差做出调整。为了避免这一问题,为积分项加入积分限幅,限制其进入积分饱和状态。
速度环采用增量式PID如式(2)、式(3)所示,其控制增量只与近三次状态有关。由于步进电机工况下受到的外在干扰因素小,所以增量式PID可以很好地满足其对速度调节的要求。
式(2)-(3)
式(2)-(3)中:Du(k)为PID输出的控制增量;u(k-1)为前一次输出量;u(k)为本次输出量。在速度环中,将位移调节器的输出量与当前电极移动速度的偏差作为速度调节器的输入量,从而自动调节PWM脉冲的频率,进而控制步进电机转速。
由于增量式PID的输出数值只与近三次测量值有关,而不是对应实际误差,即没有进行误差累加,所以该算法无需过多处理即可达到理想的控制效果。
3.2 程序设计思路
上位机借助LabVIEW进行设计,主要实现硬件状态控制与检测、电压电流采集、电弧波形显示与保存等功能。程序设计流程如图7所示,LabVIEW上位机人机交互界面如图8所示。
电弧发生装置的控制:由上位机产生步进电机运转所需的脉冲信号和方向信号,其控制策略采用基于PID控制器的闭环控制方式,在步进电机运行过程中配合压力传感器检测信号作为两电极是否完全接触的判据,配合限位开关对可移动电极运行范围进行控制,确保拉弧电极在安全区域内正常接通或分离。
主线路开关的控制:同样由上位机产生控制信号控制每一个开关的通断。电弧发生装置开始拉弧前上位机开始采集线路电流和两电极之间的电压,并在拉弧过程中实时采集拉弧过程的电压和电流信号,实验结束时,根据硬件传感器一、二次侧电压、电流变比关系将所采集到的数据换算为实际电压、电流,并在人机交互界面上显示波形,后台同步保存波形数据。电极位移数据存储程序框图如图9所示。
图8 LabVIEW上位机人机交互界面
图9 电极位移数据存储程序框图
程序的关键部分为故障电弧的发生和维持。电弧的发生基于压力传感器实现,主线路开关未闭合前,动电极进行靠近运动,当压力传感器数值达到阈值且检测到线路电流后,动电极开始分离运动。所述分离运动为电极按照设定速度和预定位移远离静电极。
电弧维持基于PID双闭环控制实现,LabVIEW程序以内部时钟为时间基准,当压力传感器数值达到阈值时电极进行远离运动,当移动到指定距离时电极开始靠近运动,依此往复,实现电弧的维持。不同等级电流的拉弧线路所设移动距离不同,其数值可经实验得出。在采集到电压波形产生畸变、电压幅值小于正常值时,表示故障电弧产生,定时器开始计时,达到设定时间后电极开始分离运动,回到初始限定位置。
4 实验测试
4.1 电弧发生模拟实验
实验现场及现象如图10所示,实验开始后,两根电极通电,在动静电极分离瞬间,产生亮眼电弧光,随着燃弧时间的延长,碳棒被烧蚀,出现发热变红的现象。
信号采集线路使用示波器进行辅助检测,确保实验数据波形的准确。在电弧发生时,信号采集模块将采集到的故障电弧数据通过高速采集卡实时传入上位机。上位机通过LabVIEW对硬件各模块在电弧发生过程中的状态值进行监测,同时上位机将采集到的信号数据以波形的形式在人机交互界面显示出来,当动电极返回原点时表示一次故障电弧模拟完成。
图10 实验现场及现象
4.2 实验分析
阻性负载线路故障前后实验波形如图11所示。
图11 阻性负载线路故障前后实验波形
由图11可见,相比于正常电流波形,故障电弧电流存在明显的零休区,即故障电弧在正常电流的过零点之前降为零,然后又在正常电流过零点之后的某一时刻快速升高。随着电弧燃烧更加炽烈,平肩现象更为明显,同时电流快速升高也代表着电弧重新燃起。由于平肩现象的产生,电流每个半周期数值都有变化,且该现象是随机的。同时,对比正常电压波形,故障电弧电压波形呈现马鞍状。经过多次实验发现,电弧的发生具有随机性和间歇性,该现象与阻性负载下的电弧理论一致。
分别进行开环控制与闭环控制各八组实验,前四组实验拉弧线路电流值为3A,后四组实验拉弧线路电流值为8A。根据采集的电压信号是否发生马鞍状畸变、幅值是否小于正常值来判断燃弧时间。由于本文装置采用压力传感器数值变化量作为电极移动的信号量,因此电极位移速度不宜过快,以避免过度挤压传感器而损坏设备。
经过多次测试可知,位移速度为0.8mm/s时,本文装置拉弧效果最为稳定,故设定该值为电极移动速度。通过调整电极移动距离,达到燃弧时间大于3s的目的。开环控制测试数据见表1,双闭环控制测试数据见表2。
表1 开环控制测试数据
表2 双闭环控制测试数据
由表1可知,开环控制时,两电极经过挤压、摩擦过程后,编码器反馈电极速度数值波动大,且误差普遍大于0.01mm/s。表2中的位移速度稳定在0.80mm/s左右,且误差小于等于0.01mm/s。
通过表1和表2的对比可以看出,在维持燃弧时间大于3s的前提下,相较于开环控制,在误差允许范围内,双闭环控制下电极位移距离无需多次调整,移动距离几乎不变,稳定可靠。该系统通过设定电极移动距离控制电弧时间,进而实现故障电弧的模拟。随着线路电流等级的提升,电极移动距离也随之增加。
由于实验条件有限,其他电流等级电弧模拟可根据实际情况对位移进行适当调整,表1、表2数据仅限当前实验环境使用。当多次进行故障电弧模拟实验之后,压力传感器初始数值会发生改变,故在装置每次挤压后,进行压力值初始化,系统监测数值清零并将当前压力值重新设定为装置起始压力值,以此来确保实验稳定可靠。
综上所述,本文装置可以实现对故障电弧现象的模拟,且在研华PCIEH高速采集卡的加持下,故障电弧数据采集完整、准确,可以满足对故障电弧模拟实验的要求。
5 结论
基于串联故障电弧的检测技术和产品检测需求,本文提出了基于增量式PID的双闭环电弧发生装置控制策略,并研制了基于LabVIEW的故障电弧模拟装置,实现了根据预设燃弧时间及燃弧距离产生稳定可靠电弧的基本目标。
本文装置具有良好的人机界面,适合进行不同电流等级串联故障电弧的特性研究,改进了常规电弧故障发生装置的结构和控制方法,提高了故障电弧模拟的成功率,可为电弧故障保护产品的开发和故障电弧理论的研究提供参考。
本工作成果发表在2023年第12期《电气技术》,论文标题为“基于位移及转速双闭环控制的故障电弧模拟装置设计”,作者为杨雨、苏晶晶。