为提高掘进作业效率和智能化程度,可借助互联网、大数据和云计算等信息化技术,针对掘进工艺、掘支运设备和集中控制系统等关键技术进行研究攻关,开发大断面煤巷快速掘进成套装备协同控制算法和软件功能模块,建设掘进工作面远程数字化集控系统。通过加强信息手段来推进煤炭生产方式的变革,降低煤矿安全隐患及事故危害,提升生产效益。
煤矿地质信息是一种随着采掘活动在时间与空间不断发生变化的四维动态信息。通过开发工作面数据模型,实现地球物理数据和随掘随采数据的自动采集、处理和解释,建立精准三维动态地质-巷道模型,实现地质、测量及生产动态信息一张三维电子图管理。应用智能探测、自动定向及导航等先进技术与装备,使掘进系统具有智能感知、自主决策和自动控制功能,实现煤矿掘进系统的智能化建设。
文章来源:《智能矿山》2023年第7期“智能采掘”专栏
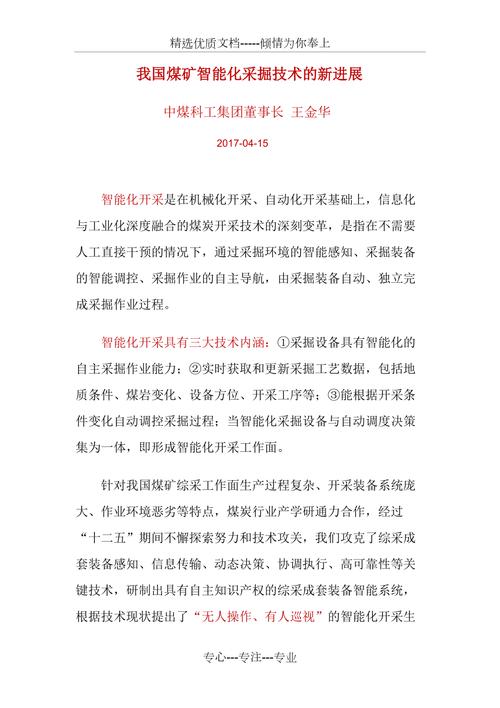
作者简介:李旭,副研究员,博士研究生,现任西安合智宇信息科技有限公司董事长、总经理,主要从事工业自动化控制和智能信息化技术研究工作
作者单位:西安合智宇信息科技有限公司
引用格式:李旭,任广燕,董博,等.煤矿智能化掘进系统建设方案探索[J].智能矿山,2023,4(7):48-54.
01 智能化控制系统架构
通过配套的智能化系统、三维地质建模、掘进机自主定位导航系统,依据地质模型驱动断面成型路径规划截割技术、负载自适应控制技术、危险区域人员识别系统及视频采集子系统,可构建智能化控制系统。其中掘锚机自动定位和导航技术是实现掘锚机智能截割的基础。通过检测掘锚机自身的位姿来实现机身定位并调整行进方向。实现自主定位和导航的主要方式有惯导、电子罗盘等,依据采掘工艺的要求自主完成整个煤岩截割过程,煤矿智能化控制系统如图1所示。抛锚机的智能截割包括实现与控制截割轨迹指定、截割滚筒转速和截割臂摆动速度,可根据煤岩特性进行适当调整。
图1 煤矿智能化控制系统总框架
远程控制系统
远程控制系统(图2)包含井下远程监控中心、地面远程监控中心和掘进机控制单元(掘进机机载智能遥控及机载智能控制箱)。
图2 远程控制系统
(1)井下远程监控中心主要负责掘进工作面所有设备、环境、人员的集中监测,协同控制人机交互的主要设备,实现智能掘进系统与其他设备的接入和逻辑控制。
(2)地面远程监控中心(图3)主要通过矿井环网将井下远控中心数据和视频画面传输至地面监控平台,并且可以通过地面远程操作台对设备进行可视化操作。针对生产管理环节,可实现信息管理、统计分析、进尺管理等,自动生成预设管理报表;对设备运行状态、环境信息、进尺信息、报警信息等关键信息进行存储,具有历史数据查询与数据曲线显示功能。
图3 地面远程监控中心
(3)掘进机控制单元可通过掘进机机载智能遥控将原有需要在操作台手动操作的电磁及电气按钮全部采用遥控器操作进行完成;机载智能化控制箱与遥控接收部分功能合二为一,与掘进机主控器进行通信同时完成数据采集,并且对附加传感器的信息进行采集。
智能化掘进数字孪生系统
数字孪生系统充分利用三维地质模型、设备物理模型、环境信息、人员信息、设备传感器、运行工况数据,在虚拟空间中完成掘进工作面实际掘进情况的映射、采场安全隐患的预警、掘进效能的预测,实现对后续掘进工作的分析与指导。
基于数字孪生的掘进系统由数字模型、物理模型和人机交互控制、人员定位、环境信息、故障告警等单元组成。数字模型主要包括三维巷道数字模型和掘进数字模型,物理模型主要为掘进样机。煤矿智能掘进系统主要通过人机交互控制单元实现,包括监测监控单元和纠偏控制模型。利用监测监控单元实现对工作面环境信息的实时感知,在提取内部巷道的空间特征参数和位置信息控制参数后,将其上传至数据库,实时显示图像和偏航角等信息,操作者将数字驱动模型映射到掘进机上实现对掘进机的远程纠偏控制。掘进工作面智能控制系统如图4所示。
图4 掘进工作面智能控制系统
采用虚实同步控制技术实现掘进机对中纠偏控制。依据动态地质模型及生产设备模型运算,实时更新工作面地质信息,结合惯导系统,获取掘进机定位定向参数,建立巷道坐标系与掘进机坐标系,驱动掘进机截割。
根据掘进机的作业情况,考虑控制模型实时计算掘进机坐标系与巷道坐标系的位置和方向,利用最大类间方差法,通过对巷道内部特征进行分析,重构巷道环境进行坐标系标定。
通过MySQL获取参数,建立偏移距离、偏航角和巷道断面形状等参数数据库,将参数数据库同3D数据库进行连接。利用3D平台将巷道模型与掘进机结合,将掘进坐标系、巷道坐标系与数据库中的位置参数进行比对,得出二者的映射关系。
根据实时模拟动态更新三维地质模型,通过将巷道口的特征与断面模型进行比对,建立巷道坐标系,基于此坐标系来计算掘进机在巷道内部的位姿参数,将参数上传到数据库,通过计算得到掘进机目前的偏移距离,将计算结果与正常掘进状态进行对比,判断是否存在超挖或欠挖情况,并在模拟的虚拟巷道中展示出超挖或欠挖状况,将读取到的参数显示在监控界面,再通过控制掘进机左右履带运动,补偿偏移距离和偏航角,完成掘进机对中纠偏。
自动截割系统
(1)掘进机机身姿态检测系统
掘进机车身姿态检测系统通过配备的微惯导传感器获得机身航向角、俯仰角、横滚角等姿态信息,并结合机身尺寸信息,通过姿态解算软件得到掘进机车身的姿态信息。其中截割头位置信息是断面自动截割成型的重要数据信息。数据通过PLC结合构建的掘进机模型可以计算得出截割机构的俯仰角α和回转角β。由俯仰角α和回转角β利用导航定位系统测量出的截割机构回转中心坐标以及掘进机设备的航向角θ来计算出截割头在巷道中的绝对位置。截割头位置计算模型如图5所示。
图5 截割头位置计算模型
(2)依据地质模型驱动断面成型路径规划截割技术及掘进机控制模式
煤矿巷道断面类型通常可以分为弧顶式、平顶式、斜顶式3种,其中复杂程度高的仅在弧线段数、直线段数和直线斜率方面有区别。基于以上特性,利用三维地质模型实时更新巷道断面模型搭建,根据断面模型,对掘进机的断面截割路径进行科学规划和研究。
断面定义及路径规划如图6所示,通过考虑巷道本身的实际条件、截割的路径和利用控制工艺,最终实现巷道断面一个循环800mm定位截割。此外,巷道断面边界还具有边界报警功能,将断面成型误差控制在15cm以内。
图6 断面定义及路径规划
远程自动截割控制(悬臂式)的实现主要是通过确定巷道断面类型、掘进工艺和截割头外轮廓等参数,从而来确定截割头的运动轨迹。考虑截割规划,利用视觉测量位姿为基础坐标点,通过控制截割头的位置和轨迹来得到掘进机各关节运动控制量。
根据煤矿巷道设计要求的宽度和高度规划截割顺序,如图7所示。掘进机掘进时按照从上至下的顺序进行截割,同时对散落在巷道两旁的浮煤进行清理,每掘进1m为1个循环,用掘进机自身锚杆钻机进行顶部锚杆施工,每完成1个循环施工,掘进机便开始前移,进行下一循环截割。
图7 掘锚机进刀方式及进刀顺序
虚拟远程控制系统示意如图8所示,当考虑选择手动模式时,则利用人机交互方式下发指令,然后传输到数据决策中心,及时获取控制指令并对掘进机的行动进行动态修正;当选择自动模式时,则通过获取到的巷道参数及掘进机自身的轨迹规划,并结合当前掘进机的位姿数据进行计算并将指令下发至数据决策中心,最后传输至PLC,通过PLC控制掘进机实现断面成形截割控制。
图8 虚拟远程控制系统示意
(3)负载自适应控制技术
由于井下的地质条件复杂多变,在井下不同区域及不同地理位置处无法找寻内部岩石硬度规律,因此,掘进机的自动截割技术应能实现根据不同地层情况实时调整速度,避免出现由于速度不匹配而导致截割效率过低或者机器振动过大的现象,以延长掘进机的使用寿命,提高工作效率。
考虑到截割速度与工况不匹配的原因主要包括截割升降油缸或截割回转油缸压力过大过小、截割电机电流过大、机身航向角变动频繁等,因此,掘进机自动截割技术的截割效率可以考虑通过负载匹配率来确定。通过计算比较参数之间的关系得到负载匹配率η,根据η合理调整目标方向的截割升降油缸电磁阀和截割回转电磁阀的控制电流,利用负载自适应控制技术实现设备的正常运行,并通过降低机器的超负荷运动来减少机器的强烈震动,以提高截割效率。
负载自适应控制逻辑如图9所示,当η>100时,降低电磁阀电流,当η<100时,则提高电磁阀电流来实现合适的负载匹配率函数。图中P1为截割升降油缸压力,P2为截割回转油缸压力,Power_M为截割电机功率,dθ为机身航向角和加速度的变化率。
图9 负载自适应控制逻辑
危险区域人员识别系统
危险区域人员识别系统主要通过图像处理和目标检测算法来识别井下工作人员,利用模块化系统和上位机界面确保综掘设备的精准响应,解决了设备开机后司机无法确认后部输送机摆动范围内有无人员的问题;并通过进行结构优化达到系统的有效性。
人员识别系统功能的实现是利用红外摄像头与图像处理相结合的办法,通过在综采设备的后部安装红外摄像头,确保摄像头能够捕捉到输送机摆动区域外半径2m内的视频信息,再通过图像处理完成人员识别,当摆动区域内有人员存在或接近时,对人员进行探测并识别,及时向司机发出提示信号,并对人员进行警告,确保井下综采设备区域人员的安全。
视频采集及数据传输系统
掘进工作面数据传输采用无线+光纤的连接形式,兼顾灵活性和稳定性,并且便于拓展基于无线的设备(WiFi/4G/5G)接入。采用双极化定向天线,适合在巷道环境中进行长距离通信。采用矿用铠装光纤,抗拉抗压性能优异,通信接头采用快速连接器形式,更换和维护方便。另外,视频采集及数据传输系统按照模块化方式进行设计,模块直接使用快速连接器进行连接,在发生故障时可以快速进行诊断与维修更换,减少因系统故障而造成的生产损失。
环境监测系统
在掘进工作面安装瓦斯、粉尘、风速等传感器,并设置环境安全监测分站(方便扩展),分站接入井下远程控制中心,实时监测工作面环境参数,可在井下及地面远程集控平台进行显示,且可根据环境参数阈值设定相应的保护和预警。
分站和地面及井下监控中心进行数据通信,可实现对各类传感器的数据采集、实时处理、储存、显示,控制与地面、井下监控中心的数据通信,具有自检功能,可实现远程断电。
02 三维地质建模
工作面建模技术
三维地质建模是地质分析和地质研究的工具,建立基于地层沉积的煤层分布工作面地质模型,根据钻探资料与不同沉积地层的空间点位置,利用隐式迭代建模算法,对煤层的空间位置展布进行空间插值,建立工作面初始静态地质模型。隐式迭代建模算法无法直接求解,主要是通过一个离散化的自然体模型,建立相互之间的联络网络,然后进行迭代计算。该方法依赖于网格节点的拓扑关系,不以空间坐标为参数,是一个无维数的插值方法。针对网格节点上ø值的估计问题,隐式迭代建模算法建立了计算网格节点最优解目标函数:
R(ø)=R(ø)+ρ(ø)
式中:R(ø)为最优解目标函数;ø为自变量;
R(ø)为全局粗糙度函数;ρ(ø)为线性约束违反度函数。通过使R(ø)达到最小,以实现2个目标:①使R(ø)达到最小,从而尽可能使在任意节点上的函数值逼近该点领域内节点的均值,使每个节点的值尽可能平滑;②将原始采样数据转化成定义在一些节点上的线性约束,使线性约束的违反度达到最小,即线性约束符合程度达到最大,从而使相关节点的值尽可能逼近采样数据。
通过对比函数插值、隐式迭代插值、克里金插值(表1),可以发现隐式迭代插值要高于函数插值和克里金插值。进一步说明了通过隐式迭代插值法建立三维工作面初始化静态模型具有明显的可行性与优越性。
表1 函数插值对比结果
地质模型动态更新技术及三维可视化
(1)模型动态更新
模型的精度是影响建模的重要因素,数据不同,建立的模型精度也会有一定差别。由于地质数据的不准确性,随着工作面不断掘进,会不断揭露新的煤层数据。新揭露的数据不断修正原有模型,常规插值算法建立的模型若要实现新揭露的数据更新模型,整个模型都需变化,而通过隐式迭代插值算法则无需变动原有模型,可在原有模型的基础上不断修正。
(2)三维可视化
工作面三维地质模型需要有一个统一的平台对其进行展示及相关功能的实现,在地质基础模型构建完成后需要开发一套地质可视化系统。该系统主要实现煤矿地质条件的可视化呈现,具体包括煤矿掘进工作面地质信息(钻孔、陷落柱、断层等)、工作面的漫游和工作面的实时推进展示等功能。工作面三维地质模型的建立,需综合利用包括地面、钻孔、井下等多种探测手段及煤矿采掘活动所获得的地质信息,以及已查明影响开采的构造条件、煤层变化及其他地质异常体,并以此构建智能开采三维地质可视化模型。
掘进工作面生产设备建模
基于大数据分析智能决策的开采模型要实现对掘进机的工况监测和掘进控制模型的要求,需要在掘进机的合适位置安装传感器。通过安装多种类传感器监测掘进工作面空间范围技术数据指标,结合工作面环境信息、运输设备工况、视频影像等,能够较为全面地反映掘进工作面的实时运行状态,以此建立掘进工作面生产运输设备模型。
03 项目方案预评分
根据国家能源局《智能化示范煤矿验收管理本办法(试行)》中I类煤矿掘进系统评分指标,采用综合评分法对项目进行打分,通过现场查验对不符合项进行适当扣分,得到最终分数(表2)。结果显示基本符合预期目标。
表2 项目方案评分
04 结论
采掘工作面智能化掘进是未来一段时期内煤炭行业技术进步的必然要求,加快建设完善智能化掘进数字控制系统,推动煤矿智能化快速发展,深入挖掘智能化数字经济,融合应用地质建模技术、大数据分析、环境扫描、惯性导航等技术,实现基于巷道掘进的常态化自动探测及采集的地质信息进行模型自动更新,以此建立基于大数据分析智能决策的掘进生产设备模型,实现“自主截割、主动支护、远程巡视”的“透明化、少人化”快速掘进作业模式,对加快现代化、智能化的煤炭体系建设具有重要意义。