电动机的效率取决于铁芯和绕组所用材料的选择、它们的物理排列以及它们在处理和组装时的小心和精度。损失可分为两类。相对独立于负载的损耗(恒定损耗),以及随负载增加的损耗(负载相关损耗)。
影响效率的因素有如下5条:
1、导体含量
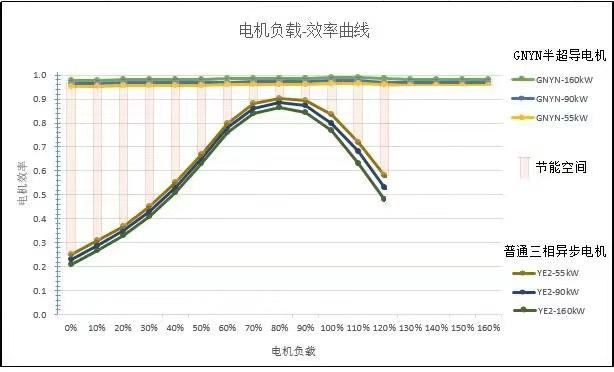
绕组中的电阻损耗随着电流的平方而增加(随负载而增加),通常约占总损失的35%。可以减少这些电阻损耗通过在绕组中放入更多的铜–使用更粗的电线–并改进制造技术以缩短端部绕组(这不会增加输出功率,但会增加损耗)。
由于更多的铜需要更多的空间,无论是在端部绕组还是在定子槽中,磁路中的材料体积将会减少,导致更早的饱和和增加的铁损。因此,有必要增加磁芯的长度,有时直径也是。
通常,增加的长度通过增加单元的非驱动端的突出来适应。因为铜损失取决于负载,增加铜含量的好处在高负载时最明显。因为铜的电阻系数为正,所以损耗随着温度的升高而增加。
图1–典型标准电机的负载损耗
2、磁钢
磁钢是电机中最昂贵的部件,因此从成本角度来看,总量的任何增加都是不可取的。铁损有两种类型——滞后损失和涡流损耗。
磁滞损耗是由于磁通密度/磁化力曲线的非线性造成的,是钢本身的一种特性,为了使其最小化,需要两种特性——低能量损耗和良好的高场磁导率,即钢必须易于磁化不得在高达1.8特斯拉的高磁通密度下饱和。
涡流损耗是由定子叠片中的感应电流引起的,通过减小叠片的厚度和确保相邻叠片之间的良好绝缘来减少涡流损耗。
图2–磁化和磁滞曲线
较薄的叠片自然生产成本更高且更难处理,因此选择的厚度总是一种折衷。当电源因谐波而失真时,磁损耗尤其重要,因为涡流损耗随着频率的平方增加,而磁滞损耗与频率成比例。
使用改良磁钢的好处是降低整个工作范围内的损耗,但是,因为它与负载无关,所以在低负载时特别明显。
3、热设计
新的建模技术使得冷却流量经过优化的电机减小的间隙(增加磁路的效率)和较低的铜损耗。较低的损耗和良好的散热设计导致较低的工作温度因此使用寿命更长。
4、空气动力学
大多数电机通过整体风扇将空气吸入绕组,然后通过外部带肋的外壳排出,从而实现冷却。气流是复杂的,已经使用了计算机建模为了优化风扇的设计和整流罩,以产生更有效的冷却和更低的噪音水平。
可以减少风阻损失通过仔细设计转子。
5、制造和质量控制
的引入电机装配期间磁钢中的应力会增加铁的流失高达50%。通过在设计阶段考虑装配技术并注意处理技术,制造过程中增加的铁损已经减少到可以忽略的程度。定子和转子之间的偏心会产生谐波通量,从而导致更高的损耗。
这些改进的总体结果是效率提高了3%(相当于损失减少约30%)和在低负荷下损失减半。图4显示了75 kW标准电机和高效电机的效率与实际负载的对比。
图4–标准电机和高效电机的效率对比
因为许多电机在低负载或空转下运行相当长的时间,所以高效率装置的设计者非常注意减少恒定损耗。
结果是加载时损失减半少于25%的负载和一个满载时效率提高3%至5%,损失减少了约28%. 这是一项了不起的成就。
个人观点,仅供参考
免责声明:本平台所发表内容及图片,标原创内容为本人原创。转载和分享的内容只以学习为目的,仅供参考,不代表本人的观点和立场。如有侵权和错误,请联系删除或修改,欢迎各位同行,共同交流学习!