齿条传动具有传动比稳定、传递动力大、传动效率高、可靠性高等优点凹,被广泛应用于钻机、升船机、海上自升式钻井平台、发动机、航天器间等设备中,齿条的加工精度直接影响着这些机械设备的正常运行。
由于齿条传动具有高刚性,受力变形小,且总刚度与行程长度无关的特点,被应用于机床的进给伺服系统,因此齿条的加工精度决定加工零件的质量。齿轮齿条机构还具有体积小,结构紧凑等优点被作为核心传动部件应用于机器人关节和机械手中,因此对齿条的加工精度要求越来越高。
随着现代工业的发展,齿条加工行业快速发展,要求齿条传动设备在提高传动效率的同时尽量减少噪音,因此需要提高齿条的加工精度。条作为齿数无穷多的齿轮同样具备齿轮的一些特性,主要采用成形法和展成法进行加工。成形法主要有铣齿加工其加工精度可达到 8 级精度。
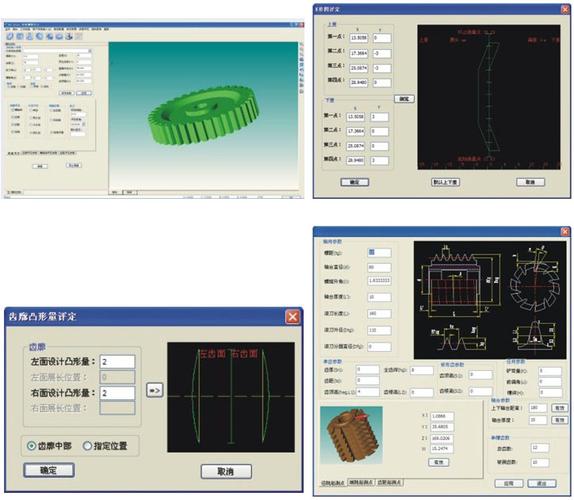
展成法主要包括插齿、滚齿、磨齿、拉齿、齿等加工工艺,其中插齿加工精度可达到 6 级精度,滚加工精度可达到 4 级精度,磨加工精度可达到 3 级精度。加工精度的提高对条检测精度和检测效率提出了更高也更加严格的要求。
在智能汽车和新能源汽车发展背景下,提出电子制动助力器和电子助力转向系统其中电子制动助力器能够提升能量回收效能,减少能源排放对环境造成的污染。电子助力转向系统可确保车辆安全性和燃油经济性。齿条作为传动机构被应用在电子制动助力器和电子助力转向系统,其加工精度影响车辆制动系统的安全性和转向系统的稳定性。
随着“以塑代钢”的提出,高分子合成材料被成功制备,塑料齿条被研制成功。塑料齿条具有重量轻、耐腐蚀、低成本、无噪音运行、更低的摩擦系数以及无需外部润滑即可运行等优点,作为汽车转向系统和智能分选装备的核心传动机构,其加工质量直接关系到所在系统的传动精度和寿命在生产实践中,齿条的加工制造和检测密切相关。
齿条检测作为质量控制的技术保证,同时也是产品验收的重要依据,对齿条的加工制造具有指导作用。目前齿条检测方法分为两种,一种是接触式测量,另一种是非接触式测量。
接触式测量具有测量精度高、技术相对成熟等优点,但相比于非接触测量效率偏低;非接触式测量可高效、准确地测量工件。相比于接触式测量,这种方法具有更高的测量效率。但是,非接触测量无法测量齿面上的一些凹形特征,由于测量仪器传感元件与被测工件之间的距离和间隔介质严重影响测量精度,导致测量精度低于接触式测量。
此外,非接触测量技术使用了大量高精度的光学和电子元件,相对接触测量价格昂贵,对工件和环境有特殊要求因此,接触式测量齿条被广为采纳。
接触式测量的测量精度主要由测量仪器的精度决定。目前,可以检测齿条的仪器包括齿条测量仪、三坐标测量仪和齿轮测量中心等。齿轮测量中心可以自动对待测工件进行测量。与传统测量仪器相比,可以实现高效率、多功能、高精度测量。
与三坐标测量机相比,可以实现多数据通道输入、多轴联动采集数据等功能。作为齿轮测量中心的核心,计算机软件系统的质量决定着整个系统的质量,再加上现代测量技术的发展将从以硬件开发为主体转化为以软件开发为主体,所以软件的设计开发和质量尤为重要。
因此,本课题基于GMC400齿轮测量中心对齿条测量软件进行设计和开发,软件的质量直接影响齿条测量的精度和效率。
齿条作为齿轮的一种特殊型式,被广泛应用于航天、汽车、石油等领域,其精度对设备的传动精度和寿命产生重要影响,因此需要根据目前生产设备和工艺技术的发展水平,采用相应的生产工艺和制造技术加工出高精度齿条。
目前,在齿条的生产加工中,大多数采用了传统的制齿工艺,如插齿、铣齿、磨齿、拉齿、滚齿、温锻和摆碾,以满足不同的需求。随着工艺制造的快速发展,齿轮成形、冷摆动碾压、冷滚打成形等制齿工艺被相继提出。
近年来,许多学者针对特殊齿条的制造提出新的加工工艺。除此之外,在“以塑代钢”的趋势下,越来越多的学者投身于塑料齿条加工工艺的研究中。插齿工艺是插齿刀用展成法上下插齿,齿条和插齿刀(与齿条合的齿轮)配合移动,而达到切削齿条毛坏的目的。
在插齿机加工齿条过程中,影响齿条加工制造和质量的因素众多,其中插齿刀齿廓精度主要影响齿条的齿廓偏差,插齿刀分齿精度和机床传动精度主要影响齿条的齿距偏差。为了提高插齿机的精度,许多学者对插齿机进行改造,并提出新的加工工艺。
湖北戴蒙德机械有限公司熊辉等对 Y54 型插齿机进行改造加工长度为 1396mm的齿条,经检测齿条的齿距累积误差为 0.lmm。济南二机床李勃等采用 SH180/300MAAG 插齿机,对模数6m,齿数 3,长度 999.026 mm,节距18.8500.013 mm 的条进行精插加工,加工完成后用三标测量机进行检测,达到6 级精度。
铣齿加工属于成型法的一类,加工设备主要包括普通卧式铣床 X6432A、YXK5140直齿数控铣床、X53K 立式床、数控专机和德国 KESEL 机等采用床对高精度齿条进行加工时,由于分齿精度和分齿行程不能满足加工要求,因此桂林机床股份有限公司的张雄德等通过对普通卧式铣床 X6432A 进行改造,加工条后经检测发现齿距累计误差在 0.07mm 内。
除此之外,张洋等通过对立铣设备 X53K 进行改造,实现了装来、定位及检测为一体的齿条加工,提高了效率的同时保证了产品的加工质量,将齿距累计误差要控制在lmm以内。
拉齿工艺是在拉床设备上进行齿条加工,具有高效率、高精度等优点。在齿条的加工过程中,其加工精度受拉刀的修磨过程的影响,因此上海采埃孚转向系统有限公司在对拉刀进行更换时,将同时更换拉刀和拉刀座,从而达到消除二次装夹拉刀引起齿廓误差的目的,同时提高了拉床的有效工作时间。
吴一芳等利用单轴高精密数控成型拉齿机,采用先粗拉刀加工,再精拉刀加工的加工工艺可加工出精确的齿廓,充分体现了拉齿加工成本低、尺寸稳定、生产效率高,加工的齿廓表面质量及精度好的特点139。
对于精度要求高的齿条,一般采用磨齿工艺进行加工,齿条磨床设备包括 MK5212数控龙门导轨磨床、齿条磨齿专机等。
齐重数控装备股份有限公司的董学哲等在MK5212 数控龙门导轨磨床上加工精密斜齿条,通过对齿数为 30,螺角为 915’10的斜齿条进行加工,并用三坐标进行测量可以达到 5 级精度,齿面及基面粗度达到0.4um,螺旋线偏差为0.008um,齿距累积误差为 0.032um401。
孙立杰等通过对数控齿条成形磨齿机进行研究,加工长度小于 lm,模数小于 20mm 的齿条,加工精度可达 6级精度1411。华中科技大学的刘畅基于数控齿条成形磨齿机,研制出砂轮修整器应用于该设备上,在保证砂轮尺寸精度的同时进一步提高了齿条的加工精度。
在机械加工和制造中,小型齿条是一种常见的传动部件,不仅加工难度大,而且精度要求高。莱芜钢铁集团有限公司的宋存等通过对滚齿机进行设计改造,加工模数小于6mm、长度小于 600 mm、宽度小于 50 mm 的小模数条,提高了小型齿条生产效率和加工精度。
变节距齿条无法采用传统工艺进行加工制造,可以采用温锻或摆碾工艺来进行齿部的加工,但温锻工艺和摆碾工艺只能加工小尺寸齿条,且加工精度有限,无法满足传动精度要求。因此,Xu 等提出了一种新的加工方法,即齿轮成形。
主要是建立了刀具与工件之间的精确包络运动模型,通过包络运动模型和刀具模型的同时求解,得到了齿条的齿廓数学模型,并提出了切削力预测方法,实现了变传动比齿条成形过程中切削力的精确预测,提高可变传动比齿条的高质量加工。
传统齿条加工方法无法满足某些高性能齿条的生产要求,Han 等提出了一种新颖的齿条加工方法一一冷摆动碾压方法,利用高动态摆动刀具在直线路径下锻造齿条的齿。结果表明,采用冷摆动碾压方法可以制造出高质量、高附加值的齿条。
Zhuang 等在有限元系统模拟软件平台上,在相同条件下分别采用冷摆动碾压和传统冷锻工艺对工件进行加工。结果表明,与传统冷锻工艺相比,冷摆动碾压工艺可以通过改变工件塑性变形的程度,提高加工工件精度。
2019 年,王雪峰等提出齿条冷滚打成形技术。把加工零件放于高速旋转的滚打机上进行连续击打和滚轧,使位于接触范围内的材料产生塑性流动,并随着进给运动的变形逐步积累,最终形成完整的高性能齿廓零件,有效解决了传统冷挤压成形所需要的高能耗、设备吨位大问题,展现出精密、高效、绿色、无污染的优势。
针对精度较高的大模数齿条加工,属于极限加工,技术含量高,且需要采用专用刀具和专用机床,导致加工成本提高。
何海洋等在加工齿条时,通过在万向铣头上安装可用刀盘加工齿条各齿廓面,使用样板控制加工尺寸的同时,运用热校直方法控制加工过程中产生的变形,提高了齿条的加工精度,这种加工齿条的方法不仅节省了专用刀具费用、优化了生产工艺,而且提高了尺寸精度,保证了产品质量。
杜志国等利用数控铁床上万能角度头改进了齿条的加工方法,将表面粗糙度控制在 1.6um 以内,齿距累积误差在 0.10~0.15mm 区间。弧形齿条由于直径大,超过滚齿机的加工范围,且在结构上存在一定的弧度,加工精度难保证。因此,杨莉等通过研究开发出一种线切割技术,并通过加工进行了验证,加工后齿廓精度达到8 级精度等级。