关键词: 临界转速 力学模型 叶轮 多体动力学 有限元 正弦泵
正弦泵(SinePump)是一种回转式新型容积泵,最早由德国MASO公司于20世纪80年代研发制造,其优良的工作性能成功解决了食品卫生行业中的浆料输送难题。相对于以往的离心泵、螺杆泵、转子泵及齿轮泵等,正弦泵最大优势就是能够在无剪切、无脉动的情况下对物料进行柔和搅拌与输送,因此被广泛应用于食品、饮料、化妆品、医药及化工等行业[1]。尽管如此,正弦泵在国内市场和相关行业的应用并未全面展开,目前针对正弦泵的专业研究和相关技术文献并不多见。
近年来,国内泵业制造厂商和相关科研人员开始重视正弦泵的技术优势,并在正弦泵的研制和行业应用方面进行了探索,例如:华南理工大学的丁问司、张旭等[2]建立了基于AMESim平台的正弦泵关键部件及整机模型,并通过仿真计算研究了正弦泵的动态特性;江南大学的陈娜、周一届[3]在Fluent环境下模拟分析了正弦泵的流场情况,同时对叶轮结构参数进行了优化设计;汉胜工业设备(上海)有限公司的陈禹等在介绍正弦泵工作原理、技术特点的基础上,对MASO正弦泵在奶制品和肉内加工行业的应用情况进行了介绍[4]。此外,我国目前已经建立了一批针对正弦泵研制的联营及合资企业,如上海汉胜设备有限公司,上海天田泵业制造有限公司、上海贝工泵业制造有限公司、温州兴盛轻工机械有限公司等[1]。叶轮组件是正弦泵的核心部件。文中以某型正弦泵结构为参考,通过转子动力学计算和多体动力学仿真分析,深入研究了叶轮组件在运转状态下的工作性能,为正弦泵的动态仿真设计提供了重要技术参考。
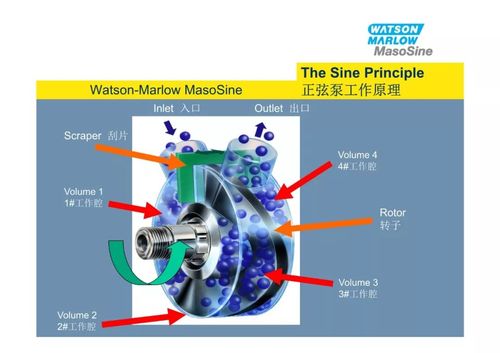
1、正弦泵结构原理
从结构特性来看,正弦泵设计精巧、拆卸方便,属于食品卫生级正位移容积泵,目前已获得多个国际权威食品卫生认证(如FDA,EHEDG,USDA,NAL等)。正弦泵系统结构组成见图1,主要包括主轴、叶轮、机座、泵壳、套筒、刮板、滑槽、衬套、轴承室及轴承。其结构及功能原理为:具有正弦曲线特征造型的叶轮与刮板沿径向卡合,并通过滑槽和泵壳共同形成封闭腔体;叶轮利用其独特的结构形状,将泵腔划分为4个相同的腔室,而卡装在叶轮之上的刮板又将泵腔隔分为吸入腔室和排除腔室,以此保证在泵壳的进出口形成压差。正弦泵通过主轴输入扭矩驱动叶轮转动,并在刮板沿滑槽运动的共同作用下实现流动物料的连续输送。
与传统的转子泵和螺杆泵相比,正弦泵具有无可比拟的性能优势。由于叶轮结构具有连续起伏的柔和轮廓造型,使得运行过程中不会对物料产生剪切作用,避免了物料发生气泡或破碎,因此通过正弦泵输送的食品物料在粘度、色泽及品质方面更胜一筹。此外,正弦泵不仅具有更高的自吸力(最高达85kPa)和排出压力(最高达1500kPa),而且其单一叶轮设计能够保证每次物料循环的输送体积流量恒定,且物料吸入和排放过程平稳、流型一致,无峰值脉动等不利影响[5]。
图1正弦泵结构
2、转子动力学特性
2.1理论基础
对于具有转盘零件的转子系统,根据转子动力学理论,可通过线位移x,y和角位移θx,θy来表征转子振动形态,其振动方程见式(1—2)[6]。式中:M为动力矩阵,是由转盘集中质量和直径转动惯量构成对角线元素的对角矩阵;J为极转动惯量矩阵,是以转盘极转动惯量为对角线元素的对角矩阵;K为刚度矩阵,是由刚度系数构成的对称矩阵;δ为位移列向量;ω为转子角速度。
将叶轮组件结构被转化为具有2个弹性支撑和1个集中质量(m)的离散转轴系统,则其动力矩阵M、极转动惯量矩阵J和刚度矩阵K均为二阶矩阵,且位移列向量可表示为:δ1=[x,θy]T,δ2=[y,-θx]T。将以上矩阵和向量元素分别代入式(1—2)便可得到正弦泵叶轮组件的振动微分方程。
2.2等效力学模型
对正弦泵叶轮组件结构进行简化处理,建立如图2所示的等效力学模型,其基本思路:利用具有不同截面属性的弹性梁单元(BEAM188)构建阶梯主轴;将叶轮结构等效为集中质量点m,并由三维质量单元MASS21模拟;主轴支撑由二维轴承单元COMBI214模拟。通过建立等效力学模型,不仅能够很好地简化和取代叶轮组件实体结构,而且很大程度上减少了转子动力学分析的复杂性及工作量,有利于节省机时、提高计算效率[7]。
图2等效力学模型
图3有限元模型
以等效力学模型为依据,在Ansys环境下利用APDL语言开发叶轮组件结构设计程序,建立如图3所示有限元模型,相关建模数据见表1。阶梯主轴段之间通过节点联接,其材质采用45钢,涉及的材料属性参数包括:密度ρ=7800kg/m3;弹性模量E=207GPa;泊松比λ=0.3。叶轮采用不锈钢材质,其质量m=1.05kg;忽略轴承质量和阻尼,其支撑刚度K=544MN/m。根据叶轮组件装配关系设置相应边界条件,令集中质量m与主轴刚性联接,完全约束COMBI214单元自由端所有平动与转动自由度,同时限制其支撑端沿轴向移动和绕轴心旋转自由度。
表1有限元建模数据
2.3模态频率及振型
正弦泵是典型的高速旋转机械,为保证整机系统性能稳定和安全运行,要求叶轮组件必须具备良好的结构动力学特性。通过模态分析能够有效预测和评估叶轮组件的固有振动特性,有利于正弦泵的减振降噪和故障诊断[8]。分别对叶轮组件、主轴及叶轮进行模态分析,提取其前6阶模态频率,并在Matlab环境下绘制频率分布见图4。分析比较可知,3种模态频率均按从小到大的趋势分布,符合结构动力学中模态频率的排序规律,其中,叶轮的模态频率最大,主轴结构次之,而叶轮组件最小,且其基频分别为4057.9,1348.6,704.61Hz。由此可知,与叶轮组件结构相比,单一实体零件的各阶模态频率显然更高,说明子零件(主轴和叶轮)的抗振性能要优于叶轮组件,因此在对正弦泵进行结构动力学设计时,应重点从叶轮组件自身结构形式或装配关系方面加以改进。
模态振型是预测结构在各阶共振频率下发生振动和形变的重要依据。由振动力学理论可知,结构的低阶模态对其振动响应更为敏感,因此在结构动力学设计过程中关注低阶振型更为有意义[9],如图5—6所示的叶轮和主轴一阶振型。分析可知,在一阶模态频率下,叶轮结构会发生较明显的弯曲振动变形,最大变形区域(4处)出现在轮廓边缘且呈对称分布;主轴一阶振型主要表现为弯曲和扭转振动变形,最大变形区域集中在两侧轴端位置。叶轮组件等效力学模型的一阶振型,三阶振型,五阶振型见图7,其中虚线为原始模型结构,分析可知,一阶振型和三阶振型均是主轴段以轴承支点为中心,在xOz面内发生的往复振动变形,而第5阶振型则表现为主轴的弯曲和扭转组合变形。
图4模态频率比较
图5叶轮一阶振型
图6主轴一阶振型
图7叶轮组件振型
2.4临界转速
在物料输送过程中,叶轮组件处于高速旋转状态,准确计算其临界转速对于正弦泵的稳定运行具有重要意义[10]。根据模态分析结果,叶轮组件基频(704.61Hz)对应的共振转速高达42276.6r/min,以此为参考设定转子动力学分析范围。考虑陀螺效应,根据式(3)所示角速度ω与转速n的转换关系,在0~80000r/min转速区间内,利用OMGA命令对叶轮组件施加一组驱动转速,每组转速间隔5000r/min,即转子动力学计算过程共包括17个载荷步。
在模态分析基础上执行各载荷步计算过程,并通过PLCAMP命令获得叶轮组件的Campbell图,见图8。由Campbell图可知,在0~80000r/min转速范围内,叶轮组件共存在三阶临界转速,即29824.36,42375.40,61274.25r/min,与之对应的转速频率分别为497.07,706.26,1021.23Hz。正弦泵的工作转速一般在600~800r/min左右,可见叶轮组件的工作转速远远小于一阶临界转速,说明在实际工况下该正弦泵完全能够按照设计转速稳定运行。
尽管如此,高速化始终是旋转机械发展的终极目标,随着近年来正弦泵的性能提升和技术进步,行业内对其工作转速的要求也愈来愈高[11]。从转子动力学方面来看,一阶和二阶临界转速对叶轮组件的影响较大,尤其是第二阶临界转速,因为其对应的工作转速频率与叶轮组件的一阶、二阶模态频率十分接近,所以在正弦泵高速化设计过程中,为使叶轮组件能够适应更高的工作转速,应尽量消除二阶临界转速带来的不利影响。
图8叶轮组件Campbell图
图9叶轮压力转化简图
3、多体动力学仿真
3.1泵体压力计算
由于叶轮结构具有特殊的正弦波形轮廓,使得物料的搅拌和输送能够连续平稳,因此正弦泵运行过程中基本不会形成脉动和剪切效应,可近似地认为封闭泵腔的压力场呈各向同性分布[12,13]。为方便多体动力学仿真计算,对泵腔内的压力进行等效简化处理[14],见图9。假设四分之一叶片面积为S,且叶面中心点到主轴中心轴的距离为L,若作用于叶片表面的压强为P,则可将物料对叶片形成的压力场转化为一个集中力F,见式(4)。
正弦泵在输送物料过程中需克服集中力F运转,因此,可将阻力F转化为作用于主轴之上的等效力矩T,见式(5)。根据文献[1],泵体压力P=0.69MPa;通过叶片CAD实体模型检测得知:S=25cm2;L=3.5cm。将各参数代入式(4—5)即可计算出等效力矩
。
3.2仿真模型构建
在ADAMS/View平台上建立多刚体动力学仿真模型,见图10。构成叶轮组件的零部件主要包括:主轴、叶轮、刮板、滑槽及轴承。其中,主轴与叶轮采用刚性联接,刮板在叶轮连续转动作用下沿滑槽往复运动,滑槽和轴承起固定支撑作用。对各零部件赋予材料特性参数,并根据叶轮组件装配关系定义相应约束和运动副[15,16]。在ADAMS/View环境下对仿真模型进行机构学验证,按照式(6)计算其自由度,其中:活动构件数量N=2,低副数量PL=2,高副数量PH=1,则由此计算出叶轮组件自由度v=1,符合机构学设计要求。
图10叶轮组件仿真模型
将负载T施加于主轴之上,重力因子方向垂直于主轴中心轴线。考虑接触特性影响,根据运动关系和材料特性,分别在叶轮与刮板、刮板与滑槽之间施加实体接触(Solid-Solid),主要接触参数包括:材料刚度(Stiffness)、材料阻尼(Damping)、力指数(Exponent)、穿透深度(Dmax)、静摩擦因数(Mu_Static)、动摩擦因数(Mu_Dynamic)等[17,18],具体参数值见表2。
3.3结果分析
运行动力学仿真过程,设置主轴驱动转速为600r/min,仿真时间为2s,计算步长为1800。在后处理模块获得刮板运动学曲线见图11。分析可知,在正弦泵叶轮组件转动一周过程中,刮板沿滑槽发生4次往复运动,泵体完成2次吸入和排放作业,当刮板运动至极限位置时,瞬时速度为0,加速度达到最大,符合正弦泵工作原理。从位移曲线可知,刮板位移行程约为25mm,且速度和加速度曲线光滑、平顺,说明正弦泵叶轮组件运转过程平稳、性能可靠。
图11刮板运动学曲线
分析图12所示接触力仿真曲线可知,在一个循环吸排作业过程(0~0.1s)中,叶轮与刮板之间的接触力出现2次峰值(约55747N),主要是由于在2次吸排瞬间叶轮表面与刮板接触力较大;而刮板与滑槽之间出现4次峰值(约17N),说明刮板在4次往复运动过程中均会与滑槽形成瞬时接触碰撞。比较可知,刮板与滑槽之间的碰撞频率较高,但其接触力峰值却远远小于刮板与叶轮,这是由于在叶轮组件运转过程中,刮板与叶轮始终保持高副线接触,而刮板与滑槽之间则处于低副面接触。
在负载转矩T影响下,叶轮组件在高速运转状态下会对支撑部件形成一定冲击。如图13所示,在主轴运转1周过程中,会对支撑轴承形成2次较大冲击载荷,且轴承2承受的冲击载荷明显大于轴承1,最大载荷值分别为51171N和24503N,这是由于轴承2距离泵壳较近,因此受到来自泵体内部的振动冲击更大,符合正弦泵结构原理和实际运行情况。
表2主要接触参数
图12接触力仿真曲线
图13轴承冲击力载荷
4、结语
作为新一代食品卫生级输送机械,正弦泵在结构和性能方面具有无可比拟的技术优势。从动力学层面出发,综合运用理论分析、结构设计、有限元分析及多体动力学仿真等手段,对叶轮组件结构及其工作性能进行了深入研究。利用等效力学模型简化了叶轮组件转子动力学计算的难度及流程,在模态分析基础上确定了临界转速,为实际生产过程中正弦泵的调速与控制提供了依据。通过多刚体动力学仿真分析,明确了叶轮组件运转过程中关键零部件的运动规律以及接触碰撞和冲击载荷变化情况,验证了正弦泵的功能原理,为其调速控制和减振降噪提供了动力学层面的技术参考。在后续研究工作中,可考虑难度更大的流固耦合仿真或机电液一体化仿真,这方面的技术探索能够更为准确地逼近实际工况,有助于全面深刻地理解和掌握正弦泵结构性能。